Main components of a Valve
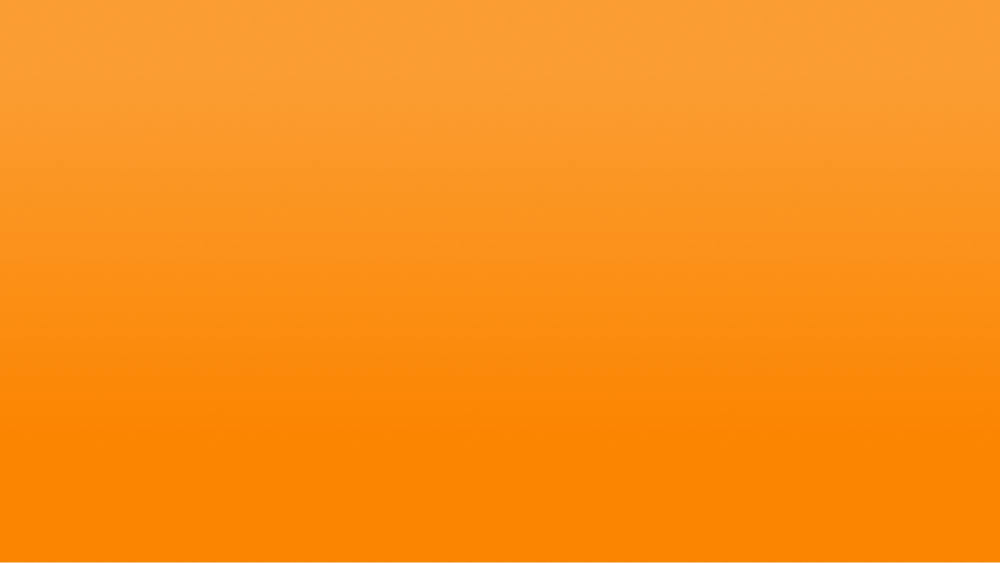
In previous articles, we became familiar with “Types of control valves”, “Valve selection guide”, “Different types of industrial valves”, “Definitions and terms in control valves” and also “Safety valves”.
In this article, we intend to examine the main components of a valve. Each valve consists of the following parts:
- Body
- Bonnet
- Stem
- Actuator
- Packing
- Seat
- Disk
- Spring
- ports
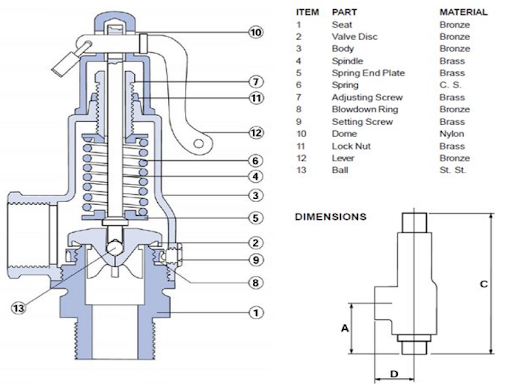
Valve body:
This part of the valve is the main component of the valve assembly because the body is the primary part that holds the components together. The body serves as the main area for the initial pressure applied to the valve, which resists the fluid pressure at the connection to the line. The inlet and outlet lines to the valve can be threaded, bolted, or welded. The valve body can be produced either by casting or forging, in various shapes. Theoretically, spherical and cylindrical shapes offer greater resistance to fluid pressure when the valve is open.
Bonnet:
The cover or casing of a valve is referred to as the bonnet, and in some designs, the body itself is made up of two pieces that are connected by bolts. Similar to valve bodies, bonnets come in various designs. Some bonnets have a simple function over the valve cover, while others serve to hold the internal components of the valves and their accessories, such as the stem, disc, and actuator. The bonnet serves as the primary pressure boundary on a valve and can be either cast or forged from the same material as the body, connected by threads, bolts, or welds. Although bonnets are necessary for most valves, they can also present challenges! Bonnet designs can complicate the valve manufacturing process, increase the size of the valve, contribute significantly to the manufacturing costs, and even be a primary factor in creating stress within the valve.
Trim:
The collection of internal components of a valve is referred to as the trim. For example, the trim includes a seat disc, stem, and bushings used to guide the stem. The operation of a valve is defined by the relationship between the position of the disc and the seat, as the trim enables the fundamental movements and controls the flow.
Disk and Seat:
For a valve with a bonnet, the disk is the third main component of the pressure range. The disk allows or prevents the flow of fluid through the valve. When the disk closes, the system's main pressure is applied across the disk. This is why the disk is considered a pressure component in valves.
Disks are typically made through forging, and in some cases, the surface of the disk is hardened to provide good wear resistance. The polished surface of the disk at the valve seat is crucial for sealing when the valve is closed. Most valves are classified based on the shape and design of the disks.
Stem:
The stem connects the actuator and the disk, allowing the disk to change position. Stems are often made through forging and are attached to the disk by welding or threading. For valve designs, it is necessary to seal the stem to prevent leakage. The presence of a smooth surface on the stem in the sealing area is very important. Additionally, the stem is not considered one of the components that fall within the pressure range.
There are generally two types of stems: one is a rising stem and the other is a non-rising stem. In the first type, when the valve opens, the stem is positioned above the actuator. This situation occurs when the stem is threaded and is created with a threaded bushing from the yoke.
In the second type, the stem does not move upward or outward from the valve. In this model, the valve disc is threaded from the inside and becomes integrated with the threaded stem.
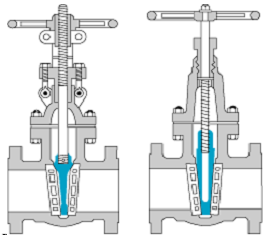
Actuator:
The actuator is the device that assembles the stem and disc. An actuator may operate manually with a handwheel or through a manual lever, motor actuator, solenoid actuator, or pneumatic or hydraulic actuator. In some designs, the actuator is held in place by a bonnet. Except in cases of controlling hydraulic valves, actuators are located outside the pressure range applied.
Packing:
In most valves, various types of packing are used to prevent leakage in the space between the stem and the bonnet. Packings are typically made from fibrous materials or other compounds such as Teflon. The packings in valves must be well-compressed to prevent fluid loss and damage to the valve stem. If the packings are loose, they can pose a safety hazard, and if they are too tight, they can damage the stem and prevent movement.
You Might Also Like
FAQs:
What types of valves are there?
There are two types of valves: rising stem and non-rising stem. In the first type, when the valve opens, the stem is positioned above the actuator, while in the second type, the stem does not move upward or outward from the valve. In this model, the valve disc is threaded from the inside and becomes integrated with the threaded shaft.
In valves, despite having several main parts, which part ultimately controls the flow?
The operation of a valve is defined by the relationship between the position of the disc or seat, as it enables the basic and primary movements as well as flow control.