Different Types of Compressors and Their Applications
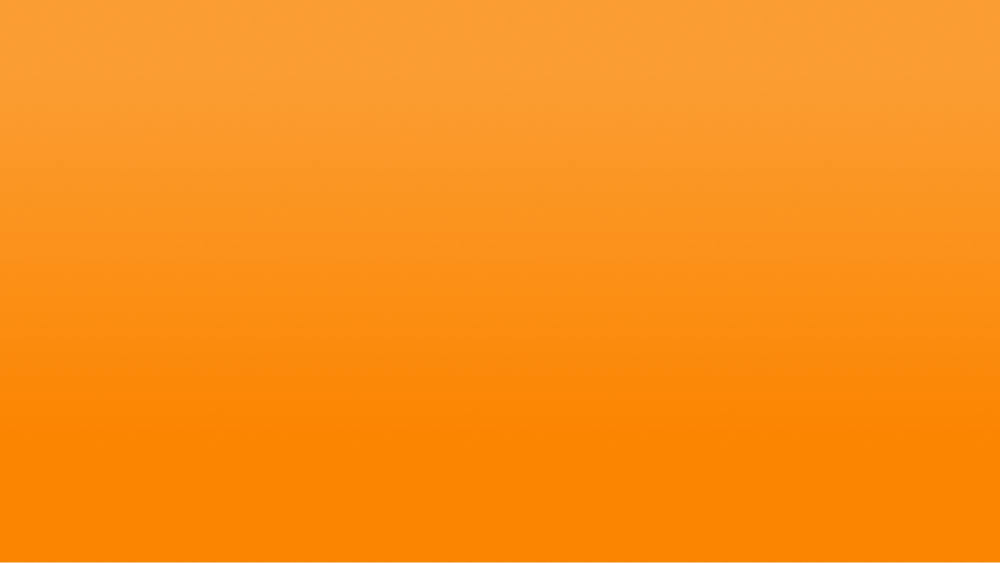
In this series of articles, we aim to introduce you to various types of compressors in several parts and explain the applications of each type available in the market. These articles are intended to provide you with a basic understanding of different compressors, and in separate articles, we will explain each type listed in this series in detail. So, join us as we delve into the world of compressors!
How many types of compressors are there?
In general, compressors are classified based on their “product volume”, and accordingly, they are divided into two categories: "positive displacement compressors" and "dynamic compressors."
"Positive displacement compressors" are machines that have a fixed output volume, while their energy or head is variable. Additionally, the gas specifications do not affect their performance.
"Dynamic compressors" are machines that have a variable output volume, but their energy or head remains constant. Furthermore, the gas specifications do impact their performance.
The Best Types of Compressors:
Each type of compressor is used for a specific application, and their use depends on the flow rate, required pressure, and characteristics of the gas that needs to be compressed.
Generally, dynamic compressors are the first choice due to their lower maintenance rates, followed by positive displacement compressors. Similarly, it can be said that reciprocating compressors are likely the last choice. The maintenance rates for these compressors are significantly higher than those of other types, and the gas they produce tends to fluctuate. However, it is important to note that the final selection of a compressor depends on their operational conditions, which will be discussed further in this article.
1) Positive displacement compressors:
Positive displacement compressors are used in low and minimal flow rates, as well as in high pressure or flows where the molecular weight of the gas is low or variable (such as hydrogen mixtures). The different types of positive displacement compressors are as follows:
1.1: Rotary vane
1.2: Rotary screw
1.3: Rotary lobe
1.4: Liquid ring rotary
1.5: Reciprocating
In the article "Types of Positive Displacement Compressors", you can find more detailed information about each type of positive displacement compressor.
COMPRESSOR TYPE |
APPLICATIONS |
Rotary vane |
For the transfer of powder - polyethylene |
Rotary screw |
Low-volume air blowers, gas turbine starters |
Rotary lobe |
Air consumption for units and instrument air |
Liquid ring rotary |
Air consumption for units, instrument air |
Reciprocating |
Gas reinjection, production and mixing of H2 |
2) Dynamic compressors:
Dynamic compressors are used in places where minimal repair requirements are necessary. In dynamic compressors, the increase in gas pressure occurs due to the increase in gas velocity caused by the rotation of the vanes. This type of compressor is employed in high flow rates and with low head. The only part where a dynamic compressor can generate more energy (head) is at lower flow rates.
The most common applications for these compressors are in air blowers, MTBE compressors, and gas turbine air compressors.
Dynamic compressors are classified into two groups:
2.1) Centrifugal compressors
2.2) Axial compressors (two-piece horizontal)
Centrifugal compressors are further divided into six different types:
2.1.1) Single-stage centrifugal (with low compression ratio)
2.1.2) Single-stage centrifugal with full gearing
2.1.3) Multi-stage centrifugal with two-piece horizontal casings
2.1.4) Multi-stage centrifugal with side inlet
2.1.5) Multi-stage centrifugal (barrel type)
2.1.6) Multi-stage centrifugal with integrated gearing
COMPRESSOR TYPE |
APPLICATIONS |
Single-stage centrifugal |
Air blowers |
Single-stage centrifugal with full gearing |
Low-rate return flows, exhaust gases, unit air |
Multi-stage centrifugal |
(Propane, propylene, ethylene, mixed gases) for cooling |
Multi-stage centrifugal (barrel type) |
Return flows, reinjection |
Multi-stage centrifugal with full gearing |
Process applications, unit air, instrumentation |
Axial compressors |
Fcc blowers and gas turbine air |
:Centrifugal Compressors; Principles of Operation
Centrifugal compressors increase the energy of a gas by increasing its tangential velocity TV. The basic operation of these compressors is very similar to that of centrifugal pumps; Gas enters the compressor through the inlet valve, and the amount of incoming gas is directly related to the degree to which the inlet valve is open or closed, which minimizes shock and turbulence entering the compressor
The impeller consists of a round hub and blades attached to it, all mounted on a rotating shaft. The impeller receives gas from the inlet valve and increases the energy of the gas as it rotates. This increase in energy is proportional to the speed generated at the blade edge UT and the tangential speed of the gas VT that change in the impeller. VR .also indicates the relative speed of the gas at the blade. The resulting speed V is a vector that is the sum of the relative speed VR and the speed at the blade edge UT
A diffuser surrounds the impeller and is responsible for gradually reducing the speed of the gas at the moment it exits the impeller. This energy diffuser converts the velocity into a higher pressure level
In multi-stage compressors, the gas exits the diffuser and enters the return vanes (on the diffuser). The return vanes direct the gas to the second stage.
Centrifugal compressors are also referred to as radial compressors because the flow exiting the impellers is radial (in the opposite direction of the axial flow).
:Horizontal two-piece axial compressors
An axial compressor consists of a main shaft with a set of rotating blades, as well as a conical-shaped casing with fixed vanes on it. Any number of blades are surrounded by a number of stator vanes. The gas enters through the inlet valve and then moves to the outlet spiral. The inlet spiral not only accelerates the gas flow but also directs it towards the stator vanes. The stator vanes completely redirect the gas flow in line with the blades.
Additionally, the blades increase the gas energy by increasing its speed. The stator vanes act like a trumpet, creating resistance against the gas flow, which reduces the speed of gas flow and increases its pressure. Furthermore, the stator vanes properly position the gas flow for the next row of blades. Since the blades and stator vanes are arranged sequentially along the casing, the gas is accelerated multiple times before exiting the compressor, or its acceleration is reduced. Each time the gas flow strikes the stator vanes, the pressure is increased. Ultimately, the gas exits through the outlet spiral and the outlet valve of the compressor
In the article "Introduction to Different Types of Dynamic Compressors", you can find more complete and precise information about the various types of dynamic compressors
:General Points About Compressors
*Compression with positive displacement compressors is defined as the increase of gas due to the operation of a fixed volume in a confined space. Types of these compressors are categorized into reciprocating, rotary lobe, rotary screw, and rotary liquid piston.
*In reciprocating compressors (which are positive displacement), gas will not enter the cylinder until the pressure inside the cylinder is less than the suction pressure, and conversely, gas will not exit the cylinder until the pressure inside the cylinder is greater than the discharge pressure.
*Characteristics of positive displacement compressors include a fixed volume and the ability to produce variable pressure. It should be noted that in positive displacement compressors, pressure relief valves must be used to prevent pressure or power increases; otherwise, it can lead to irreparable damage to the compressor.
*In comparing axial and centrifugal compressors (the two main types of dynamic compressors), it is always observed that a 10 percent increase in head (energy) in centrifugal compressors is equivalent to a 30 percent increase in head in axial compressors.
Conclusion:
Air compressors can generally be classified into two categories: positive displacement and dynamic compressors. Reciprocating compressors and various types of rotary compressors fall under the positive displacement category, while dynamic compressors have two main subcategories: centrifugal and axial.
We learned that "positive displacement compressors" are machines whose output has a fixed volume, while their energy or head is variable. Additionally, the gas characteristics do not affect their performance. We also learned that "dynamic compressors" are machines whose output has a variable volume, but their energy or head remains constant, and the gas characteristics do influence their performance.
Furthermore, we covered points regarding the selection of the best compressor and learned about the general applications of each category of compressors.
You Might Also Like
FAQs:
How many units of head increase in centrifugal compressors are equivalent to one unit in axial compressors?
Each unit increase in head (energy) in centrifugal compressors is equivalent to a 3-unit increase in axial compressors (a conversion rate of threefold).
How many types of centrifugal compressors do we have?
Generally, there are six types of centrifugal compressors, which include single-stage centrifugal compressors (with low compression ratios), single-stage centrifugal compressors with full gearing, multi-stage centrifugal compressors with two-piece horizontal casings, multi-stage centrifugal compressors with side intake, barrel-type multi-stage centrifugal compressors, and multi-stage centrifugal compressors with integrated gearing.
On what basis are compressors classified?
The primary and most recognized classification of compressors is based on their "product volume", which categorizes compressors into two groups: positive displacement compressors and dynamic compressors.