Dynamic Compressors and their types
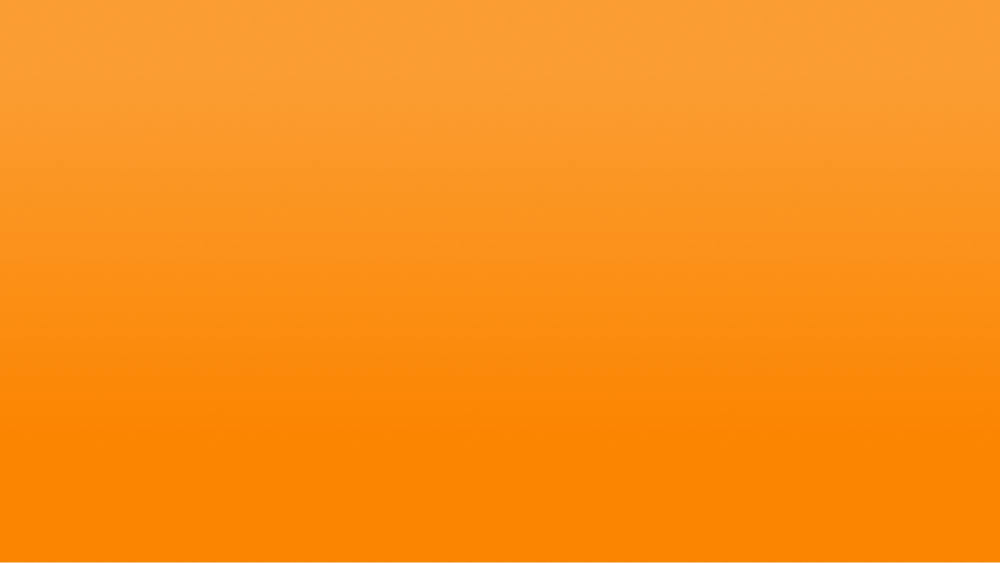
Dynamic Compressors:
In the different types of compressors article, we became familiar with different types of compressors and learned that, in general, compressors are categorized into two groups:
- Positive displacement compressors
- Dynamic compressors
We also examined the various types of positive displacement compressors in the types of possitive displacement compressors article.
In this article, we intend to explore the different types of dynamic compressors, review how each one operates, and learn some key points about this type of compressor.
What is a dynamic compressor and how does it work?
Dynamic compressors refer to a type of air compressor that has multiple blades and rotates at very high speeds. In these devices, air is drawn in between the rotating blades of the impeller, which increases its velocity. The gas or air is then discharged from a diffuser that converts the kinetic energy of the air or gas into pressure.
This type of compressor, unlike positive displacement compressors, is used for high flow rates and has various industrial applications. Compressors can increase the pressure of fluids and compress them in two main ways: by reducing volume and increasing velocity. Positive displacement compressors compress fluids by reducing volume, while dynamic compressors perform this task by increasing velocity. The transfer of energy to the fluid in dynamic compressors is continuous, and as mentioned, they are used at low pressure and higher flow rates. Unlike positive displacement compressors that operate with a constant flow, these compressors work at a constant pressure, and their performance is influenced by external conditions.
Essentially, dynamic compressors operate based on thermodynamic principles. As mentioned, in the first stage, air enters the compressor chamber through the inlet. When the air passes through the blades of the impeller, these blades impart kinetic energy to the air, resulting in an increase in its velocity due to this energy transfer. Then, the diffuser connected to the dynamic compressor converts the air's velocity into pressure, and subsequently, the high-pressure air is discharged through the compressor outlet.
Different Types of Dynamic Compressors:
In general, dynamic compressors are classified into two categories:
- Centrifugal Compressors
- Axial Compressors (two-piece horizontal)
Centrifugal compressors themselves are further divided into single-stage and multi-stage types. A single-stage centrifugal compressor consists of a single impeller with accompanying blades and a diffuser. The compressor's compression ratio capability primarily depends on the impeller's peripheral speed and blade geometry. Generally, a single-stage compressor can achieve a compression ratio of up to 3 to 1. The flow capacity of this type ranges from 1000 cfm to 300,000 cfm. Sometimes, centrifugal compressors are also referred to as radial compressors because the flow exiting the impellers is radial (as opposed to axial direction).
Single-stage centrifugal compressor (with low compression ratio):
In the figure below, you can see an example of single-stage centrifugal compressors. Sometimes these compressors are referred to as single-stage protruding compressors because the impeller of these compressors is located outside their radial bearing.
Single-stage centrifugal compressors with full gears:
The figure below shows a cross-section of these compressors. Single-stage centrifugal compressors with full gears are of the linear type, which, similar to a pump, is driven by a motor from within a gearbox. These compressors are used for low flow rates with high energy (high head). They can operate at high speeds (8000-34000 rpm), and their power is approximately 400 HP.
Multistage centrifugal compressor with two-piece horizontal casings:
The figure below shows an example of a multistage compressor with two-piece horizontal casings. The casing is divided into upper and lower parts along the horizontal centerline of the compressor. The horizontal casing design allows access to the internal equipment and components of the compressor without causing issues with the alignment between the casing and the shaft, thanks to the alignment of the bearings. If possible, the discharge pipes should be placed on the lower half of the compressor casing to facilitate the assembly of the compressor without removing the process lines.
Multistage centrifugal compressors with side inlet:
These types of compressors are exclusively used for cooling and refrigeration services. The only difference in the compressor shown in the figure above is that the compressed gas is taken from the side nozzles. An example of a refrigeration compressor is shown in the figure below. It is important to note that this type of compressor can exist in either a two-piece horizontal or a two-piece radial configuration.
Multistage centrifugal compressor (barrel type):
An example of a multistage compressor, a two-piece radial centrifugal type, is shown in the figure below. The compressor casing is a complete cylinder, and its end is movable to allow access to the internal components.
Multistage radial centrifugal compressors with multiple pieces are commonly referred to as cylindrical (barrel) compressors.
The application of cylindrical (barrel) compressors is similar to that of multistage centrifugal compressors with a two-piece horizontal casing; however, in standard applications, cylindrical compressors are chosen for higher pressure applications or gas mixtures with lower molecular weights (such as hydrogen gas mixtures).
Multistage Centrifugal Compressor with Integrated Gearing:
The figure below shows a four-stage centrifugal compressor with integrated gearing.
Centrifugal compressors with integrated gearing have a low-speed bull gear that drives two or more small gears (pinions) at high speed. The impellers are positioned at one end or at both ends of each pinion. Each impeller has its own separate and unique casing, which is bolted to the casing of the large gear. The large gear casing may be designed as a two-piece horizontal unit for access to the gears. Gas flows from the inlet valve of the first stage towards the impeller. The impeller receives the gas from the inlet valve, dynamically compresses it, and discharges the compressed gas into the diffuser. The diffuser surrounds the impeller and gradually reduces the speed of the gas exiting the impeller. The output gas from the diffuser exits through a spiral casing. The spiral casing collects the gas, further reduces its speed, and creates some additional kinetic energy within it.
The gas exits the first stage through the outlet valve and enters the internal cooler, from which it is connected to the second stage. The output of the second stage enters an internal cooler and then proceeds to the third stage.
Horizontal two-piece axial compressors:
As we have explained in our other articles, axial compressors consist of a main shaft (central shaft) with a set of rotating blades, as well as conical-shaped casings with fixed vanes mounted on them. In this type of compressor, the rotors move the fluid flow, while the stators (which are fixed in place on the central shaft) increase the pressure and redirect the flow from a spiral state to parallel to the axis.
In these compressors, the alternating increase and decrease in gas velocity is a natural occurrence.
These compressors provide continuous flow and generate compressed gas in large volumes, offering high efficiency.
Axial flow compressors have various applications, particularly in gas turbines. They are also a suitable choice for environments that require high gas flow and volume. It is worth noting that these devices typically have low to medium output pressure.
Pros and cons of Dynamic Compressors:
Like other types of compressors, dynamic compressors have various features, capabilities, and advantages, the most important of which can be summarized as follows:
High efficiency in various industries
Less friction, resulting in longer lifespan and durability
A suitable option for environments that require high pressure
Less wear and tear due to the use of fewer components in design and construction
High efficiency and performance compared to positive displacement compressors
Cost-effective maintenance and repair compared to positive displacement compressors
Less vibration in dynamic compressors, eliminating the need for foundations and groundwork
However, dynamic compressors, alongside all the features and advantages they offer, also have disadvantages such as high initial costs, lack of coverage for low capacities, complex control panels, high sensitivity, and more.
The Most Important Applications of Dynamic Compressors
Dynamic compressors have numerous applications due to their efficiency and performance, the most important of which include:
Heavy machinery
Gas industry
Power generation plants
Automotive industry
Aviation industry and jet engines
Petrochemical industries
Various manufacturing and production industries
Production of various cooling and heating equipment
Of course, when purchasing these compressors, it is essential to pay close attention to factors such as the type of project, the power and capacity of the compressor, the pressure level, the volume of air produced, the size and dimensions of the compressor, the manufacturer's brand, installation and maintenance costs, noise production levels, and more.
What are the influencing factors on the price of dynamic compressors?
Given the variety and multitude of air compressors, their prices can be affected by various factors, the most important of which can be summarized as follows:
Performance
Power rating
Capacity
Pressure level
Dimensions and size
Price and currency fluctuations
Quality of compressor manufacturing
Warranty period of the compressor
Compressor cooling system
Brand and manufacturer of the compressor
You Might Also Like
FAQs:
What are radial and centrifugal compressors?
A radial compressor is the same as a centrifugal compressor. In fact, sometimes centrifugal compressors are also referred to as radial compressors because the flow exiting the impellers is radial rather than axial.
What is the compression ratio and flow capacity of single-stage centrifugal compressors?
Generally, a single-stage compressor can achieve a compression ratio of up to 3 to 1. The flow capacity of this type ranges from 1,000 cfm to 300,000 cfm.